INFORMATION DETAILS
A rock wool and its production method and process using metallurgical waste and blast furnace slag as raw materials
Author:Dongli Time:2024-01-08 15:04:43 Click:143
Background technology for preparing rock wool from blast furnace slag:
Melted blast furnace slag is one of the main by-products of blast furnaces. Usually, each ton of molten blast furnace slag contains (126-188) × A sensible heat of 104kJ is equivalent to the energy of 30-40kg of heavy oil, and it has a high temperature of about 1450-1600 ℃, making it a high-quality waste heat resource with high recycling value
At present, the main method used in China to produce rock wool is the cupola method, which is an inorganic fiber made from natural growing rocks such as basalt, diabase, andesite, etc. through melting and fibrosis. It has the characteristics of light weight, low thermal conductivity, non combustion, moisture-proof, suitable price, corrosion resistance (based on actual reports), good chemical stability, and good sound absorption performance. Therefore, it is widely used in building filling insulation, sound absorption, sound insulation, oxygen concentrator and cold storage cold insulation, and various thermal equipment filling insulation The existing rock wool production process mostly uses natural growing rocks such as basalt, diabase, andesite, etc. as basic raw materials, and uses silica, dolomite, etc. as auxiliary materials to adjust the acidity coefficient. After adding a certain amount of coke, it is melted and mixed in a cupola, and then produced into cotton using a four roll centrifuge system. The main drawbacks of this process are: 1) it requires a large amount of energy such as coke and coal, and each ton of rock wool requires about 0.6-0.7 tons of coke and other fuels. After combustion, dust pollution is severe, and if equipped with a flue gas treatment system, the cost will significantly increase; 2) Natural growth rocks such as basalt, diabase, and andesite are required, which consume a large amount of natural growth resources, cause environmental damage, and increase production costs; 3) It is necessary to melt raw materials such as cold rocks, which consumes a large amount of energy The specific content is as follows: using molten blast furnace slag as raw material, mining tailings as conditioning agent, using two-stage electric furnace heating, and setting up a nitrogen injection system at the bottom of the furnace. After excellent homogenization and conditioning, the slurry is shaken into 3-5 micrometer mineral wool filaments by a centrifuge, which are collected by a cotton collector and deeply processed into mineral wool products. The invention has the following problems: firstly, it only states that mining tailings are used as additives, and the physical and chemical properties such as raw material moisture are not clear. If the tailings particles are too coarse, the moisture content is too high, and the chemical composition is unreasonable, it will have a significant impact on the blast furnace slag melting process for producing slag cotton, which will lead to a decrease in product quality, an increase in production costs, and even cause explosion accidents; Secondly, injecting nitrogen gas into the melt in the melting furnace will cause a suitable decrease in the temperature and speed of the melt, which requires additional electrode heating and wastes a lot of energy The specific content is as follows: hot blast furnace slag is directly introduced into the initial melting zone of the slag furnace through the slag tank, and the quenched and tempered materials and hot blast furnace slag are synchronously entered into the initial melting zone of the slag furnace. The melt temperature in the initial melting zone is maintained at 1400-1500 ℃, with a holding time of 4-6 hours, and then enters the main melting zone. The melt temperature in the main melting zone is maintained at 1420-1450 ℃, with a holding time of 6-9 hours, and then enters the discharge zone, Then it flows onto the rollers of the centrifuge to form the raw cotton. The invention has the following problems: the slag furnace includes the initial melting zone and the main melting zone, and is not separated. If the blast furnace slag experiences a prolonged interruption, the entire production process needs to be stopped, resulting in serious energy waste and low production efficiency. Moreover, the heating process for adding materials in the initial melting zone is variable, and the insulation process in the main melting zone is stable. When placed in the same electric furnace, there is interference with each other, resulting in increased power consumption and higher production costs. In actual production, it is less commonly used and has poor practicality Therefore, in the existing technology, the production process of rock wool urgently needs to solve problems such as high raw material costs, high energy consumption, serious pollution, and high energy consumption A production method for rock wool using metallurgical waste and blast furnace slag as raw materials, comprising the following steps:1) Introduction of blast furnace slag: The blast furnace slag is introduced from the slag ditch on the blast furnace platform, and the temperature and fluidity of the blast furnace slag are protected during the introduction process, allowing it to flow directly into the electric furnace outside the platform. The temperature of the blast furnace slag received inside the electric furnace is ≥ 1250 ℃
2) Melt preheating: Using an electric furnace heating system, the blast furnace slag is heated to 1350-1490 ℃, with a viscosity of ≤ 1Pa · S, to protect the fluidity of the blast furnace slag 3) Preparation of mixed melt: Add metallurgical waste additives to the blast furnace slag, continue heating, and achieve temperature increase and mixing of the mixed melt through the action of electromagnetic force; Then, the mixed melt is transported to the holding furnace through the lower flow port of the electric furnace, and the mixed melt is homogenized and clarified in the holding furnace; The final temperature of the mixed melt is 1320-1420 ℃, and the viscosity is 1-3Pa · S4) Rock wool drawing: The mixed melt in the insulation furnace is directed to the cotton making system, and the fibers are made by a four roll centrifuge with an average diameter of ≤ 7.
μ M's rock wool A production method for rock wool using metallurgical waste and blast furnace slag as raw materials, comprising the following steps:1) Introduction of blast furnace slag: The blast furnace slag is introduced from the slag ditch on the blast furnace platform, and the temperature and fluidity of the blast furnace slag are protected during the introduction process, allowing it to flow directly into the electric furnace outside the platform. The temperature of the blast furnace slag received inside the electric furnace is ≥ 1250 ℃
2) Melt preheating: Using an electric furnace heating system, the blast furnace slag is heated to 1350-1490 ℃, with a viscosity of ≤ 1Pa · S, to protect the fluidity of the blast furnace slag. Enable it to have the conditions for achieving fusion and homogenization of the melt and additives at a suitable speed 3) Preparation of mixed melt: Add metallurgical waste additives to the blast furnace slag, continue heating, and achieve temperature increase and mixing of the mixed melt through the action of electromagnetic force; Then, the mixed melt is transported to the holding furnace through the lower flow port of the electric furnace, and the mixed melt is homogenized and clarified in the holding furnace; The final temperature of the mixed melt is 1320-1420 ℃, and the viscosity is 1-3Pa · S During the electric furnace production process, molten iron is discharged through the bottom outlet every 1-2 months. Molten iron comes from the iron oxide in the additive and the iron reduced by carbon in the electrode. If it is not discharged, it will cause erosion and erosion to the refractory material of the slag furnace body, affecting the service life of the electric furnace4) Rock wool drawing: The mixed melt in the insulation furnace is directed to the cotton making system, and the fibers are made by a four roll centrifuge with an average diameter of ≤ 7.
μ M's rock wool During the cotton production process, mist like dustproof oil and water-soluble thermosetting phenolic resin used as a binder can be sprayed onto the rock wool fibers. After processing and forming, rock wool is widely used in products such as rock wool boards, rock wool felt, and rock wool pipes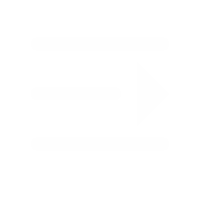
—— Tel:+86-13930107143
—— Contacts:Mr Wang
—— Add:Wei San Road South, Hope New Area, Mengcun Hui Autonomous County, Cangzhou City, Hebei Province