INFORMATION DETAILS
What are the common types of blast furnace slag?
Author:Dongli Time:2024-05-11 08:04:15 Click:61
Germany began using blast furnace slag in 1862. After the mid-20th century, the comprehensive utilization of blast furnace slag developed rapidly. Japan had a utilization rate of 85% in 1980, the Soviet Union had a utilization rate of over 70% in 1979, and China had a utilization rate of 83% in 1981.
classification
Air-cooled slag
Also known as hot slag or heavy slag. A partition wall is built from the floor to the furnace platform in front of the blast furnace to form a slag splashing pit. After the slag is discharged from the furnace, it flows into the pit through a slag ditch and is spread into a thin layer of about 15 centimeters. After being cooled by water spray, it solidifies and is excavated. After being crushed and screened, it is made into crushed stones and slag sand to replace natural sand and gravel. It is used as concrete, reinforced concrete, and prestressed reinforced concrete aggregates with a working temperature of less than 700 ℃. It is also used as a heat-resistant and anti-skid paving material for highways, racing tracks, airplane runways, railway ballast, pit filling and foundation cushion filling, sewage treatment medium, etc. This type of slag crushed stone is called "versatile engineering aggregate".
Granulated slag
Also known as water quenched slag or water slag. After quenching with a large amount of water, slag can be made into fine-grained water slag mainly composed of glass body. It has potential hydraulic cementitious properties, which can be demonstrated under the action of activators such as cement clinker, lime, gypsum, etc., making it a high-quality cement raw material. More than 80% of blast furnace slag in China is made into granulated slag every year, which is used as a cement mixing material. About 70% of the cement produced nationwide is mixed with different amounts of granulated slag. According to the Chinese national standard GB175-77, adding 15% granulated slag is required to produce ordinary Portland cement; GB1344-77 stipulates the addition of 20-70% granulated slag to produce slag silicate cement. Mixing granulated slag can save energy by 20-40% and reduce costs by 10-30%. The commonly used water quenching process uses water with a pressure of 1.5-2.5 kgf/cm2 and a dosage of 5-10 times the slag amount to be quenched in front of the furnace. Granulated slag can also be used as insulation material, fine aggregate for concrete and road engineering, soil improvement material, and so on.
Expanded slag
Each ton of slag is treated with about 1 ton of water, which can expand into porous bodies. After crushing and screening, it becomes expanded slag and can be used as lightweight aggregate for concrete (with a unit weight of 400-1200 kg/m3). The production of expanded slag includes pool method, spray pit cutting method, centrifuge method, launder method, inverted launder method and other processes. Many countries produce expanded slag. Expansion beads, also known as slag balls. In 1953, Canada developed a process for producing expanded beads. The production process involves installing a drum in front of the furnace with a diameter of 1 meter, a length of 2 meters, and a speed of about 300 revolutions per minute to disperse the slag and throw it out for about 20 meters. Under the centrifugal force of the drum and the rapid cooling effect of water and air, the slag forms particles (with a diameter of less than 10 millimeters) containing micropores, smooth surfaces, and varying sizes, known as expansion beads, with a bulk density of about 1 ton/m3. Expansion beads are high-quality lightweight aggregates for concrete, which can save 20% of cement compared to using expanded slag; It can also be used as cement mixing materials, road materials, insulation materials, wet milling or wet grinding slag, as well as materials for stabilizing foundations and improving soil. The particle size of expanded beads is smaller than that of hot splashed slag and expanded slag, and generally does not require further crushing and processing. The production of expanded beads has the advantages of simple equipment, fast cooling, fast site turnover, and convenient operation. Compared to water quenching slag, the water used for making expanded beads is more economical, and the amount of steam and hydrogen sulfide emitted is less. It causes less environmental pollution and does not require wastewater treatment. Therefore, countries such as China, the United States, Canada, France, and the United Kingdom all pay attention to adding this type of process equipment when constructing or renovating blast furnaces.
Slag cotton
By using compressed air or high-pressure steam to blow fine slag streams, slag wool can be produced and used as insulation, sound-absorbing, fire-resistant materials, etc. Direct injection of blast furnace slag is a simple process with less investment, but the quality of slag cotton is difficult to ensure. Using slag as the main raw material, adding silica, basalt, andesite, and sometimes lime as a modifier can be used. After melting and blowing, high-quality slag cotton can be obtained. Many countries are producing slag cotton.
In addition, blast furnace slag can also be used as a raw material for cast stone, microcrystalline glass, fertilizer, enamel, ceramics, etc.
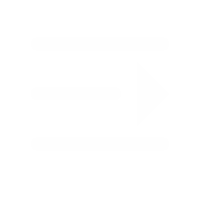
—— Tel:+86-13930107143
—— Contacts:Mr Wang
—— Add:Wei San Road South, Hope New Area, Mengcun Hui Autonomous County, Cangzhou City, Hebei Province