INFORMATION DETAILS
Construction of wall rock wool insulation
Author:Dongli Time:2024-01-17 14:45:49 Click:171
Construction of wall rock wool insulation:
Rock wool is a commonly used exterior wall insulation material in buildings. It has many advantages such as light weight, low processing cost, stable performance under various environmental conditions, and good air permeability. The editor will explain to you the construction process of rock wool insulation board exterior wall.
1. Construction preparation
First clean the base layer and confirm that the surface of the base layer is dry, smooth, and free of looseness, cracks and other quality defects. Secondly, during the construction stage of exterior wall rock wool board insulation, it is necessary to protect the outdoor ambient temperature from being lower than 5°C. After that, it is strictly prohibited to carry out exterior wall insulation construction on rainy days. If the weather changes suddenly during construction, it is recommended to cover the construction site with plastic sheeting, stop construction, and carefully check the locations that are watered by rainwater.
2. Specific construction technology
(1) Pop up the control line and hang the reference line: First, clean and level the base surface of the exterior wall. Only after passing the inspection can the insulation construction be carried out. Secondly, according to the construction design and thermal insulation construction technical requirements, pop up the horizontal and vertical control lines, expansion joints and decorative joints of external doors and windows on the wall. Then, vertical reference steel wires are hung at the large corners of special parts such as building exterior walls, and horizontal reference steel wires are hung at appropriate locations on each floor. Its function is to control the verticality and flatness of the rock wool board.
(2) Rock wool board interface processing: adjust the deviation of rock wool board specifications and appearance dimensions within a limited range. In the early stage of pasting the insulation board, a surface treatment layer should be made on the surface of the rock wool board. The specific method is: apply an adhesive with a thickness of about 1mm on the surface of the rock wool board, and use a stainless steel flat scraper to scrape the mortar layer so that the glue is embedded in the fibers of the rock wool board. When it is observed that the dry humidity of the treatment layer is suitable, the process of applying cloth glue can be started.
(3) Cloth glue: Apply cloth glue to the back of the rock wool board. There should be no adhesive on the sides of the rock wool board. For small rock wool boards with gaps between boards ≤1mm, height difference between boards ≤1.5mm, and width <300mm, it is recommended to use the full glue method.
(4) Paste rock wool boards: During the project reconstruction stage, rock wool boards should be pasted horizontally from bottom to top. During the entire process of the above operations, the continuity of the bonding between the insulation board and the base surface of the exterior wall should be maintained. Board seams should be dense and adjacent board surfaces should be smooth. The longitudinal staggered joint length of the upper and lower rows of rock wool boards should be 1/2. If it is difficult to meet the above standard requirements, staggered seams with a width greater than 200mm should be reserved. For rock wool boards covered with glue, they should be pasted on the base surface of the exterior wall at an appropriate speed to avoid glue formation and reduce the bonding effect.
After the rock wool board is attached to the wall, it should be leveled with a 2m ruler to ensure that the flatness and bonding stability of the board meet the design requirements. In the process of pasting the exterior corners and corners around the window frame, capturing the reference line is the basic work to confirm that the verticality of the upper and lower corners can be accurately controlled and controlled. At the four corners of door and window openings, it is recommended to cut the entire rock wool board into an "L" shape and lay it. Splicing is strictly prohibited. The distance between the joint and the hole should not be less than 200mm.
(5) Treatment of the plastering interface of the rock wool board: 24 hours after the rock wool board is pasted, the plastering interface is required to be processed. Specifically, a layer of adhesive of appropriate thickness is applied to the surface of the rock wool board and scraped flat with a stainless steel scraper to promote the process of embedding the glue into fiber filaments. After natural drying, the next step of plastering construction can be carried out.
(6) Mortar batch coating surface layer plastering: Specifically, after laying the mesh cloth in the previous process, plastering mortar is applied. The thickness of the plastering mortar is 1-2mm. After the large plates are scraped in batches, use small plates for leveling to protect the flatness to meet the design requirements, and control the flatness/verticality of the surface layer to ≤4mm. After the plastering mortar construction is completed, natural curing should be no less than 3 days.
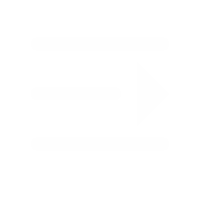
—— Tel:+86-13930107143
—— Contacts:Mr Wang
—— Add:Wei San Road South, Hope New Area, Mengcun Hui Autonomous County, Cangzhou City, Hebei Province