INFORMATION DETAILS
Technical Difficulties in Using Blast Furnace Slag to Produce Mineral Wool
Author:Dongli Time:2024-01-17 15:00:23 Click:172
Technical Difficulties in Using Blast Furnace Slag to Produce Mineral Wool
Mineral wool is an excellent energy-saving insulation material and is widely used in industrial insulation, heat insulation, sound insulation, building energy saving and decoration industries. In recent years, building energy conservation, building fire protection (based on actual reports), and building sound insulation and noise reduction have become the focus of people's attention. Mineral wool products with fire protection (based on actual reports) and sound-absorbing functions have attracted more and more attention, and market demand The speed is suitable for improvement.
Conventional mineral wool production mainly uses the cupola process, which not only consumes high energy but also causes high pollution. It is a technology that has been strictly restricted and eliminated by the state. 80% of the heat required for the direct production of mineral wool from blast furnace slag can come from the sensible heat of the slag. The energy consumption is about 30% of that of the cupola furnace process. The product cost is only 60% to 80% of that of cupola furnace mineral wool products. It is high The cotton yield of slag is above 70%, which means it has strong market competitiveness.
Blast furnace slag conditioning test
Mineral wool production has the following requirements for the melt: ① The ingredients are in the mineral wool formation area, can be dissolved within a certain temperature range (usually 1400~1500°C), and the viscosity is low at the corresponding temperature; ② During the mineral wool fiber formation The viscosity of the culture body changes slightly near the temperature; ③ It is not easy to crystallize within the temperature range of the mineral wool process; ④ The performance of the generated mineral wool meets the requirements; ⑤ The composition of the solution is uniform, confirming that the product quality is stable; ⑥ Minimize consumption and emissions, and reduce production costs , conducive to protecting the environment.
Blast furnace slag has a low acidity coefficient and cannot be directly used to produce mineral wool. It needs to be tempered. The quenching and tempering test was carried out on a 300kg induction furnace. Based on the blast furnace slag and according to the designed different acidity coefficients, the amount of silica sand added is calculated, and the slag viscosity with different acidity coefficients after conditioning is measured to provide a basis for the selection of melt components in the cotton making process. Tests have shown that when silica sand is added to blast furnace slag, it can form a uniformly mixed melt under sufficient heating and stirring conditions.
The viscosity of the slag gradually decreases with the increase of temperature, but the slope of the change is different: when the acidity coefficient is low, the viscosity curve is smoother, especially above 1390°C, the change of melt viscosity with the increase of temperature is very small, indicating that The viscosity of the slag is not sensitive to changes in temperature and has a wide temperature adaptation range; as the acidity coefficient increases, the slope of the melt viscosity curve increases, and slight fluctuations in temperature will lead to larger changes in the melt viscosity, and the curve becomes The value is steeper; under the same temperature conditions, the greater the acidity coefficient, the higher the viscosity. When the low acidity coefficient is less than 1.44, a melt with a viscosity of less than 2.0pa.s can be obtained by controlling the temperature at around 1400°C to meet the needs of the cotton making process, while the melt with a high acidity coefficient needs to be heated to a higher temperature. Just enjoy better liquidity.
Generally speaking, the higher the acidity coefficient, the more stable the chemical properties of mineral wool are. However, when the acidity coefficient is too high, it is difficult for the charge to melt. In order to give full play to the cost advantage of producing mineral wool from blast furnace slag, the acidity coefficient of mineral wool is controlled within 1.4. If mineral wool products with a higher acidity coefficient are produced, more auxiliary materials need to be added during slag conditioning, and the energy consumption of the melting system will be higher. The higher the production cost, the higher the production cost will be. Therefore, the acidity coefficient is controlled between 1.2 and 1.4, resulting in excellent product quality and low cost.
At present, the hot slag used to make cotton from hot slag in China is mainly blast furnace hot slag, silicon-manganese alloy hot slag, and nickel-iron alloy slag. After it comes out of the blast furnace or submerged arc furnace, it is transported to the electric furnace workshop through transfer and poured into the electric furnace. Its main function is to store hot slag, heat up and keep the slag warm, and protect the stability of the flow stream. Electric furnace smelting is mainly about electricity consumption. Based on the electric furnace transformer 3200KVA electrode diameter φ400mm, furnace shell diameter φ5800mm, furnace diameter φ3900mm, electric furnace rated capacity 35 tons, the monthly electricity consumption per ton of mineral wool is 450 degrees per ton of cotton (the data comes from the user's actual production data ) is much lower in energy consumption than cupola cold rolling.
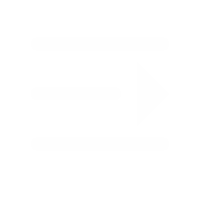
—— Tel:+86-13930107143
—— Contacts:Mr Wang
—— Add:Wei San Road South, Hope New Area, Mengcun Hui Autonomous County, Cangzhou City, Hebei Province